Handling modular timber elements: what resins can do
Strength tests conducted by Rothoblaas and Marlegno
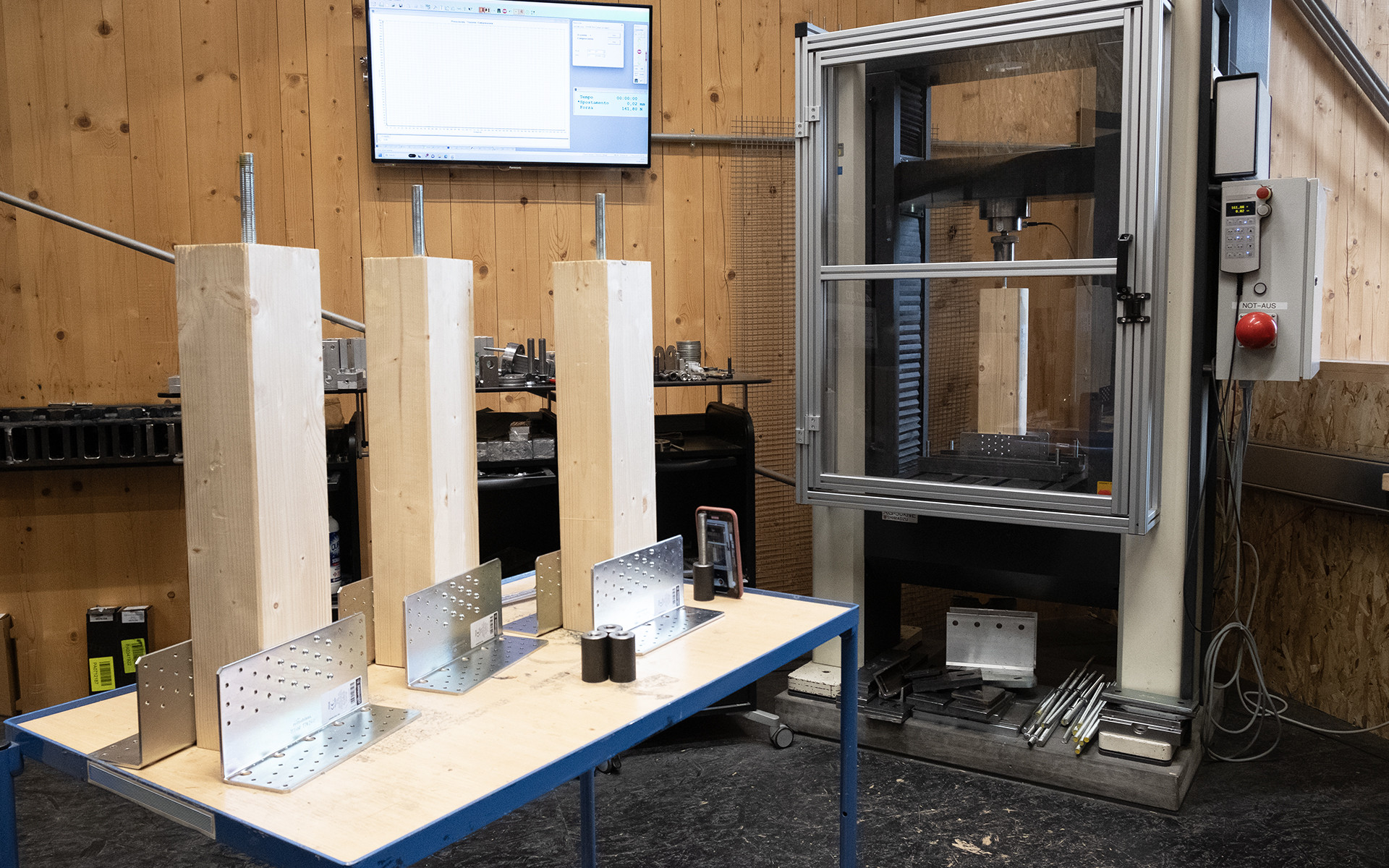
"Give me a lever and I shall move the world" said Archimedes of Syracuse. "Give us a resin and we shall move timber" is the answer from Rothoblaas, who, in partnership with Marlegno, conducted a series of tests to assess the effectiveness of using XEPOX epoxy resin to handle modular timber construction elements.
Marlegno, a leading Italian timber construction company known for its integrated approach to design, production and construction, offers tailored end-to-end solutions, including after-sales support and facility management. The company needed to test a special module handling system, which would ultimately be used to develop new residential bio-neighbourhoods with a modular system. The aim was to ensure the identified solutions could bear heavy loads during handling, even when installed on timber columns or frames with smaller cross-sections.
These structural elements require unconventional solutions, and XEPOX resin, with its advanced adhesive properties, can play a key role.
The testing took place in the MATERIALS LAB at Rothoblaas' Cortaccia facility using the 50 kN tensile testing machine installed in the test centre, with the aim of determining whether the resin could not only meet but also exceed expectations in terms of strength and reliability.
For the tests, 10x12 cm or 12x12 cm timber cross-sections were used, with tension applied by means of 8.8-grade steel metric threaded rods inserted into pre-drilled holes in the timber, filled with resin using XEPOX FLUID cartridges.
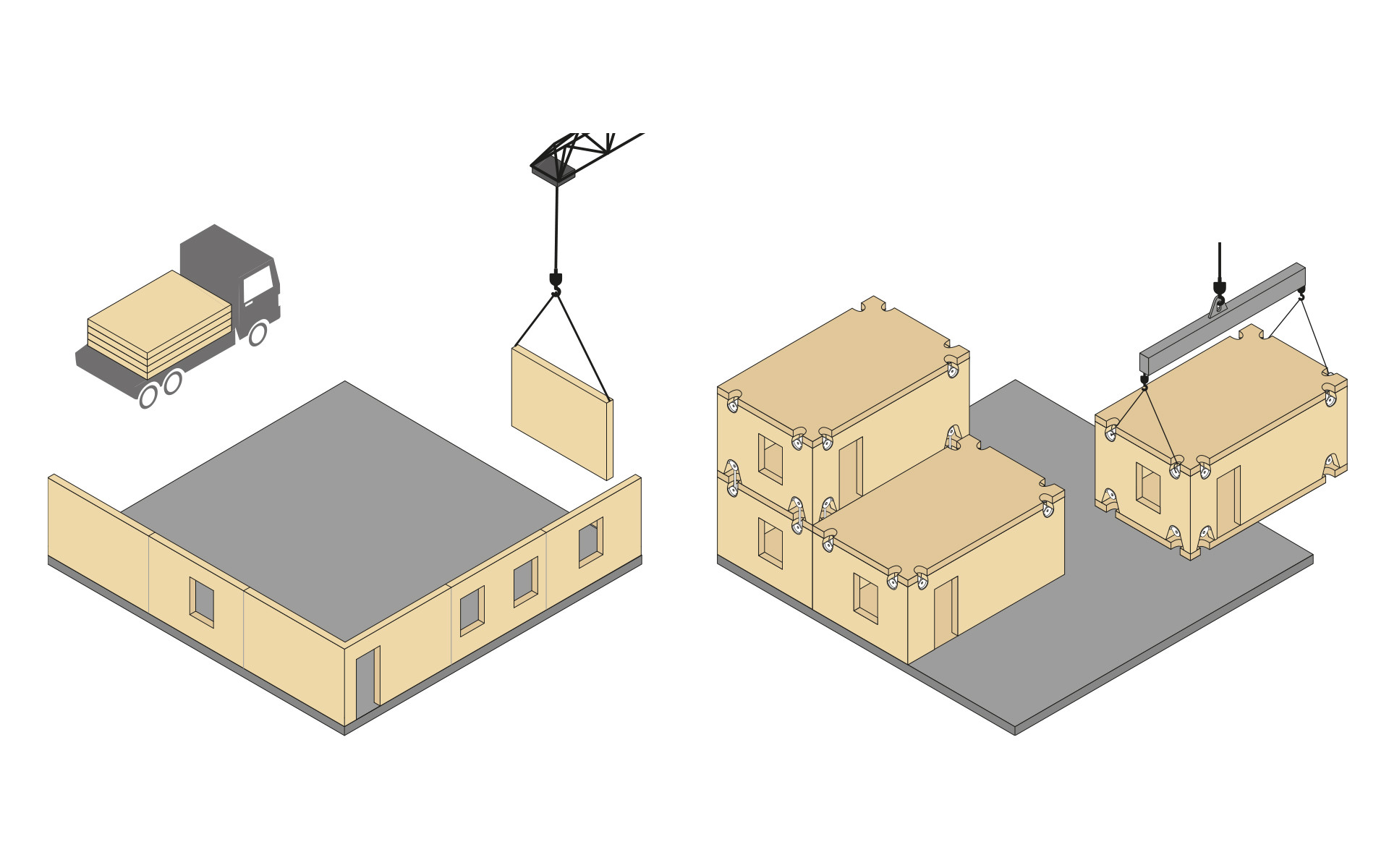
The concept of Design for Assembly (DfA) is becoming increasingly pivotal in the construction industry. It focuses on the design of elements that can be easily assembled and disassembled, thus simplifying both logistics and transport.
This approach is particularly well-suited to timber construction, where the material’s light weight helps speed up the building process.
However, transporting large elements like walls or entire rooms, both on site and within the construction area, poses significant load-related challenges, even with timber.
Timber-mounted transport hooks are typically used for larger CLT or GLULAM modules, but when lifting solutions need to be applied to columns or frames with smaller cross-sections, traditional systems are often unsuitable due to the minimum spacing requirements or limited strength.
Where does XEPOX resin come into play? Its excellent adhesive properties and mechanical strength make it ideal for these demanding situations, enhancing the tensile strength of threaded rods, which can also be inserted in smaller timber columns.
The Design for Assembly (DfA) concept is no longer just a trend but an essential practice in today’s construction industry, especially in timber construction.
While factors such as lightness, sustainability and ease of assembly are key advantages, they must be carefully balanced with the need to ensure strength and safety, even during handling. Rigorous testing is thus required to ensure high resistance.
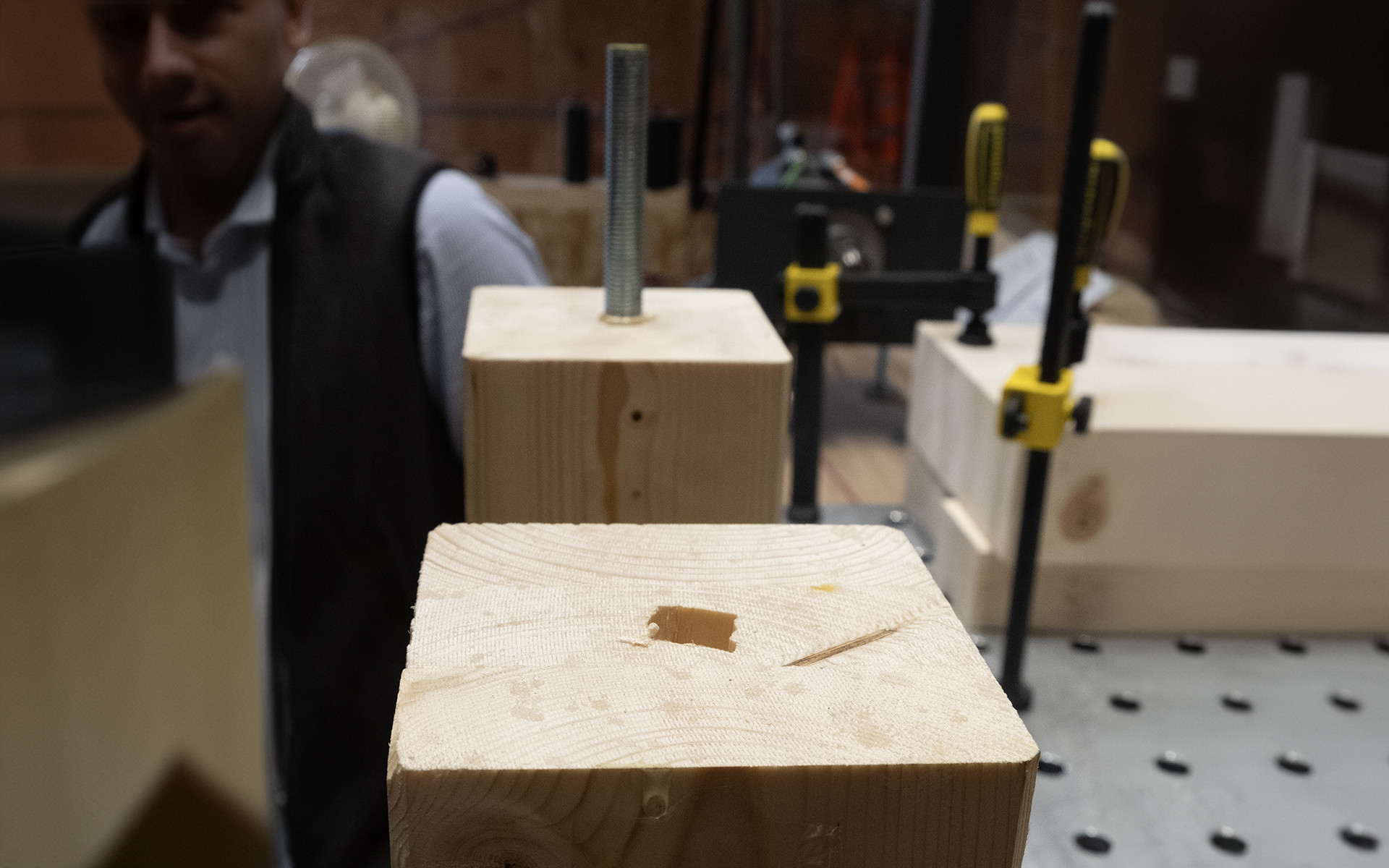
Test setup
The test consisted of 18 tensile tests, organised into six different configurations, with three repetitions for each type. The materials used included GL24h timber columns of various dimensions, along with 8.8-grade steel threaded rods inserted into holes of varying diameters to inject the resin.
The test types were structured as follows:
Test No. 1 (Specimens 100 A3-101 A2-102 A1):
Configuration: M12x200 on GL24h 10x12 cm column (fir).
Hole: 14 mm in timber.
Anticipated strength: 22,8 kN.
Specifics: The test was terminated at 50 kN to assess the overstrength under normal conditions.
This procedure included “fatigue” strength tests, with five repeated pulls on the same specimen (A1 No. 102) to evaluate the potential formation of cracks or fractures following repeated lifting.
Test No. 2 (Specimens 200 B3-201 B2-202 B1):
Configuration: M16x360 on GL24h 10x12 cm column (fir).
Hole: 18 mm in timber.
Anticipated strength: 47,3 kN.
Test No. 3 (Specimens 300 C3-301 C2-302 C1):
Configuration: M16x250 on GL24h 10x12 cm column (fir).
Hole: 18 mm in timber.
Anticipated strength: 38,1 kN.
Specifics: The aim was to exploit the utmost capacity of the lifting eye nut, which has a maximum load limit of 4 tonnes.
Test No. 4 (Specimens 400 D3-401 D2-402 D1):
Configuration: M18x360 on GL24h 12x12 cm column (fir).
Hole: 22 mm in timber.
Anticipated strength: 53 kN.
Specifics: Assessment of strength at close to 50 kN, despite exceeding the machine's maximum tensile capacity.
Test No. 5 (Specimens 500 E3-501 E2-502 E1):
Configuration: M20x250 on GL24h 12x12 cm column (fir).
Hole: 24 mm in timber.
Anticipated strength: 47,6 kN.
Specifics: Possible configuration for final lifting.
Test No. 6 (Specimens 600 F3-601 F2-602 F1):
Configuration: M16x80 on GL24h 12x12 cm column (fir).
Hole: 24 mm in timber.
Anticipated strength: 10,4 kN.
Specifics: Specimen brought to failure in all three tests to assess and estimate its overstrength.
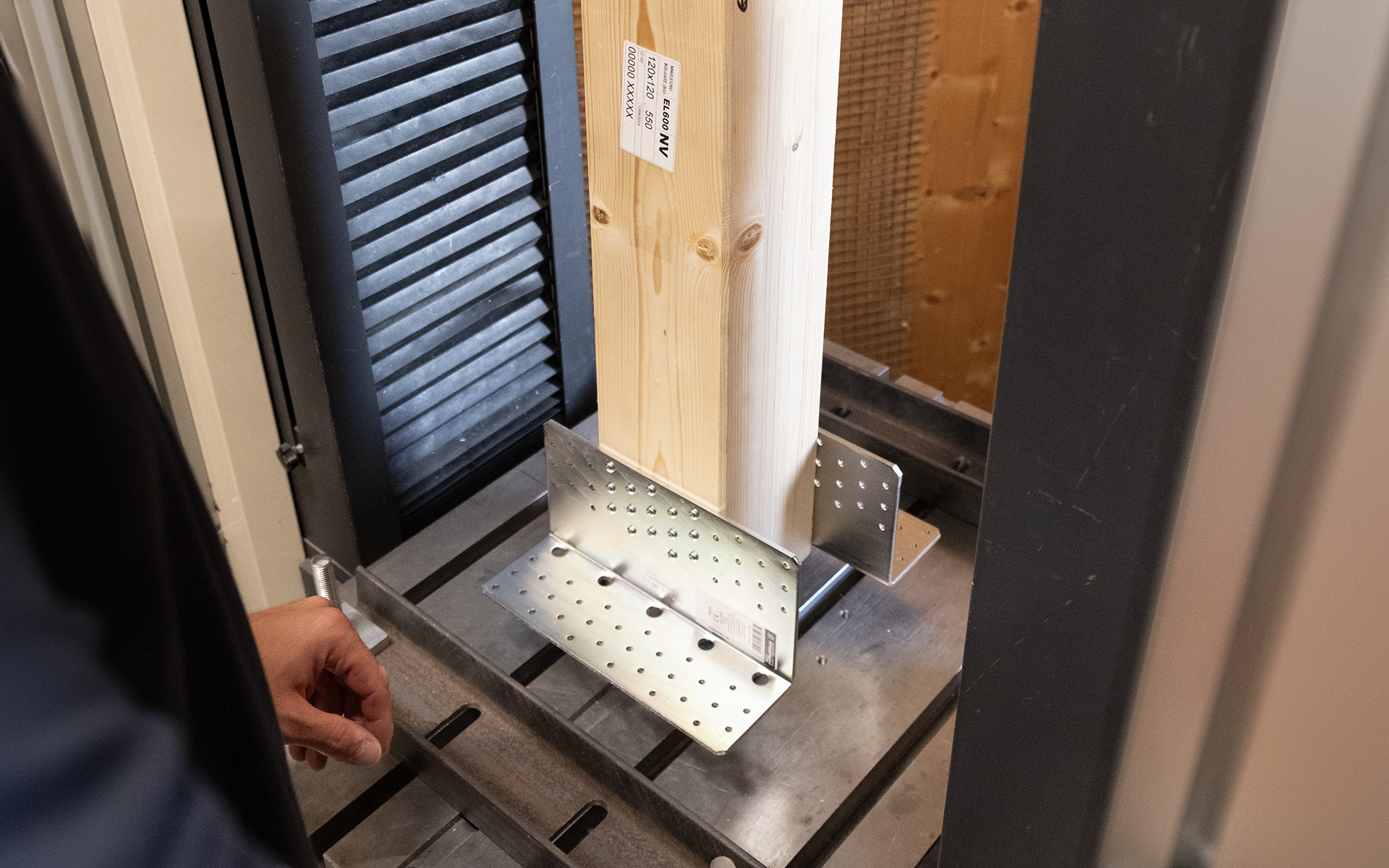
For each test, XEPOX resin was injected into the pre-drilled holes, following installation guidelines that included cleaning the holes, controlled humidity (below 18%) and ensuring the ambient temperature was between 10 and 35 °C.
Once the threaded rods were inserted, the specimens were left to cure for at least seven days before conducting the tensile test.
The setup involved positioning two TITAN V angle brackets on either side of the specimen, secured to the base of the machine using two steel C-profiles to stop it from lifting.
In accordance with the standard, the test duration needed to be 300s +-120s, i.e. a minimum of 3 minutes per test. The test speed was therefore set to a displacement rate of 1.5mm/minute, approximately 200 seconds per test.
Test Results
The test results were extremely positive, with the XEPOX resin performing better than expected. In particular:
Test No. 1: The maximum strength was 26,5 kN, significantly surpassing the anticipated 10,4 kN, with a maximum displacement of 1.78 mm.
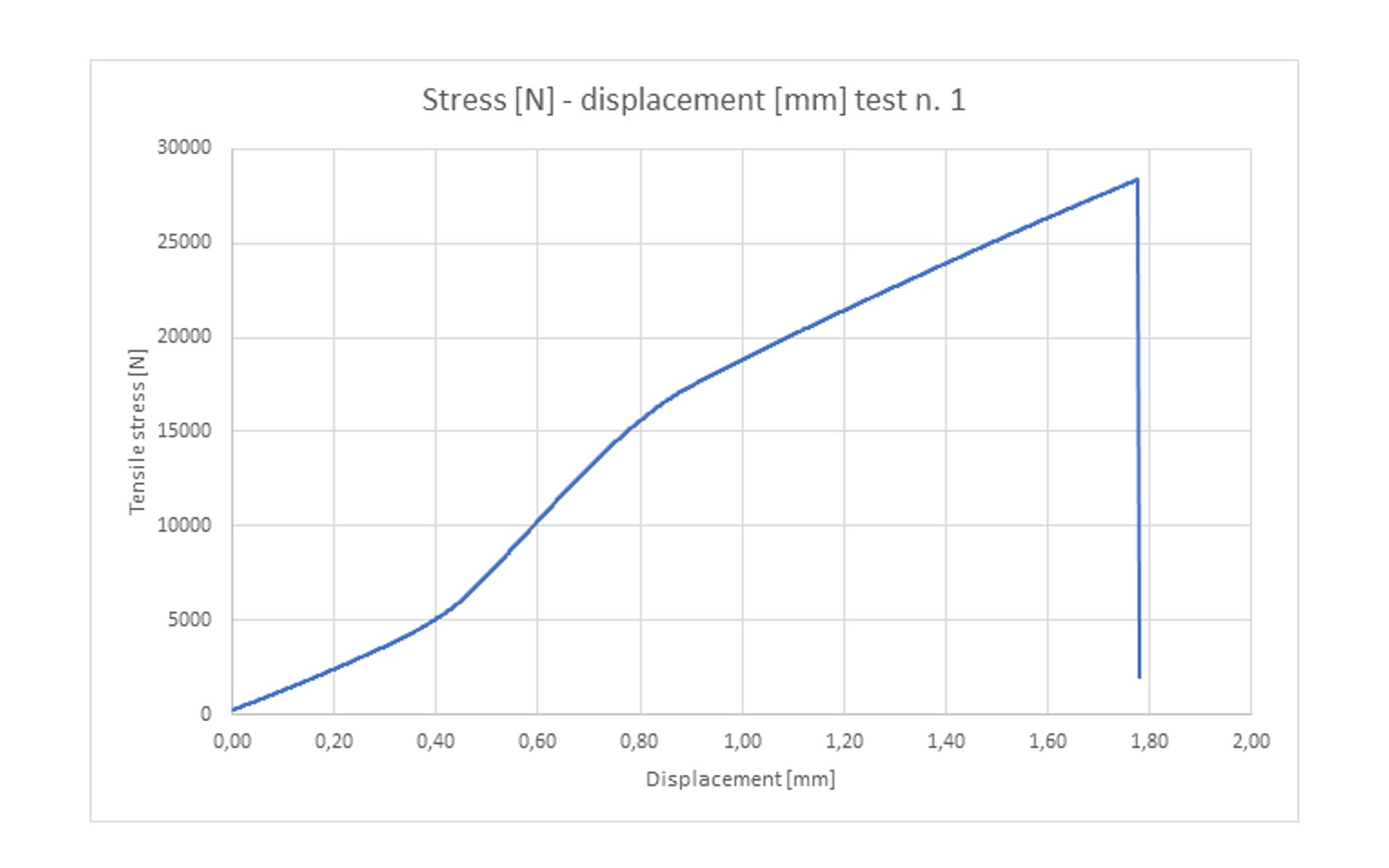
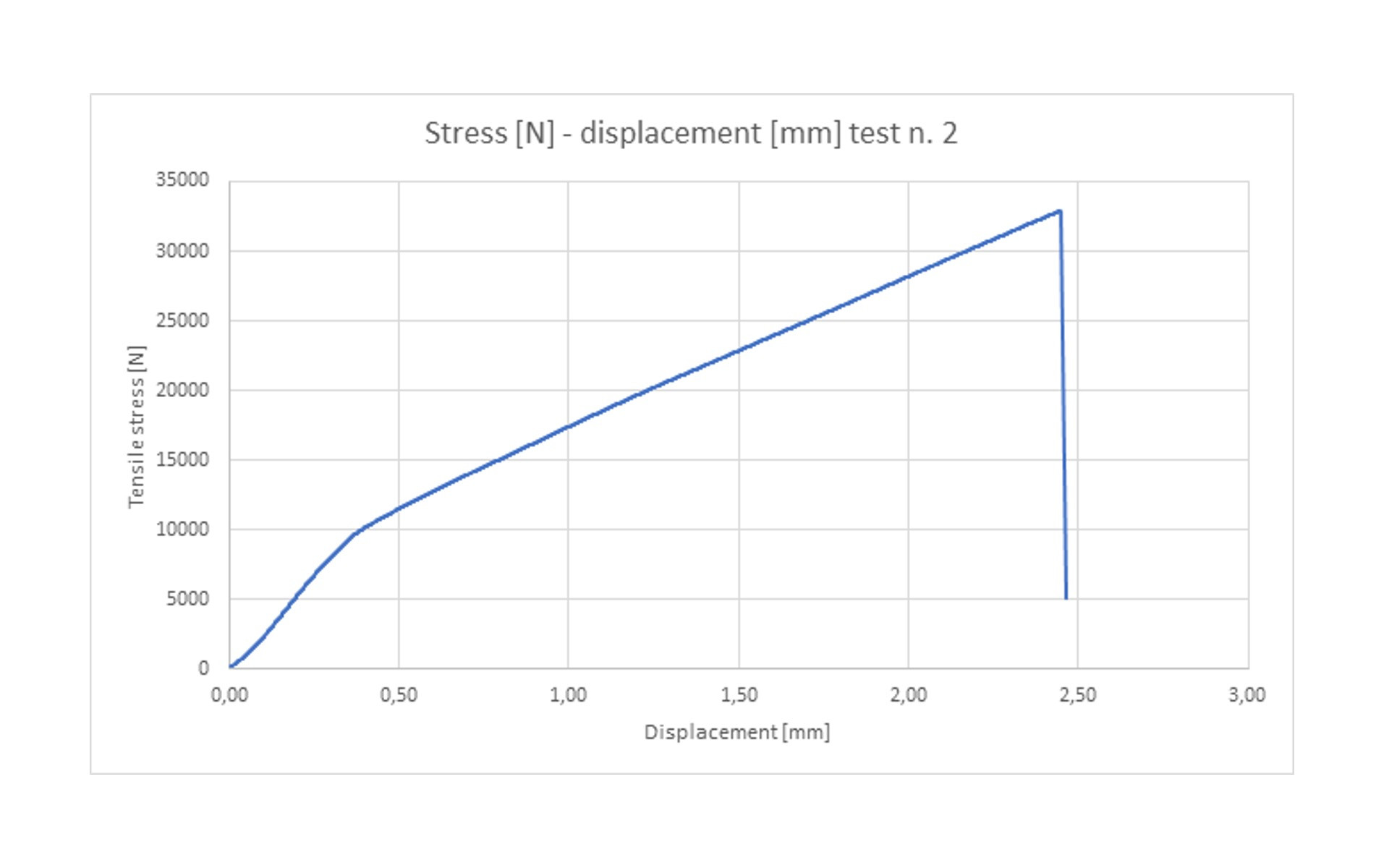

The average overstrength factor was 2,54, meaning that the rods, designed to withstand 10.4 kN, reached an average breaking value of 29 kN across the three tests. Looking at the characteristic values, that is, considering only the 5th percentile, a characteristic strength value of 20,2 kN was observed, with an overstrength factor of 1,95.
These results demonstrate that XEPOX resin can comfortably exceed the expected stresses, providing a strong and reliable solution for handling timber modules. The fact that failure occurred in the timber element, not in the resin, further confirms the system’s effectiveness.

What else can be handled with resins: The Abu Simbel temple
One of the most remarkable examples of using resins in complex projects is the relocation of the Abu Simbel temple in Egypt in the 1960s.
During the construction of the Aswan Dam, the entire temple complex had to be moved to protect it from the waters of the Nile.
This highly delicate and intricate operation involved dismantling and reconstructing the temple, stone by stone.
The strength and stability of epoxy resins played a crucial role in safely transporting the stone blocks using steel rods secured to their outer surface, ensuring the precise reconstruction of the temple in its original form.
This unprecedented feat not only preserved a monument of inestimable historical and cultural value, but also showcased the importance of epoxy resins in complex engineering applications.
For more information on this extraordinary project, visit this page.
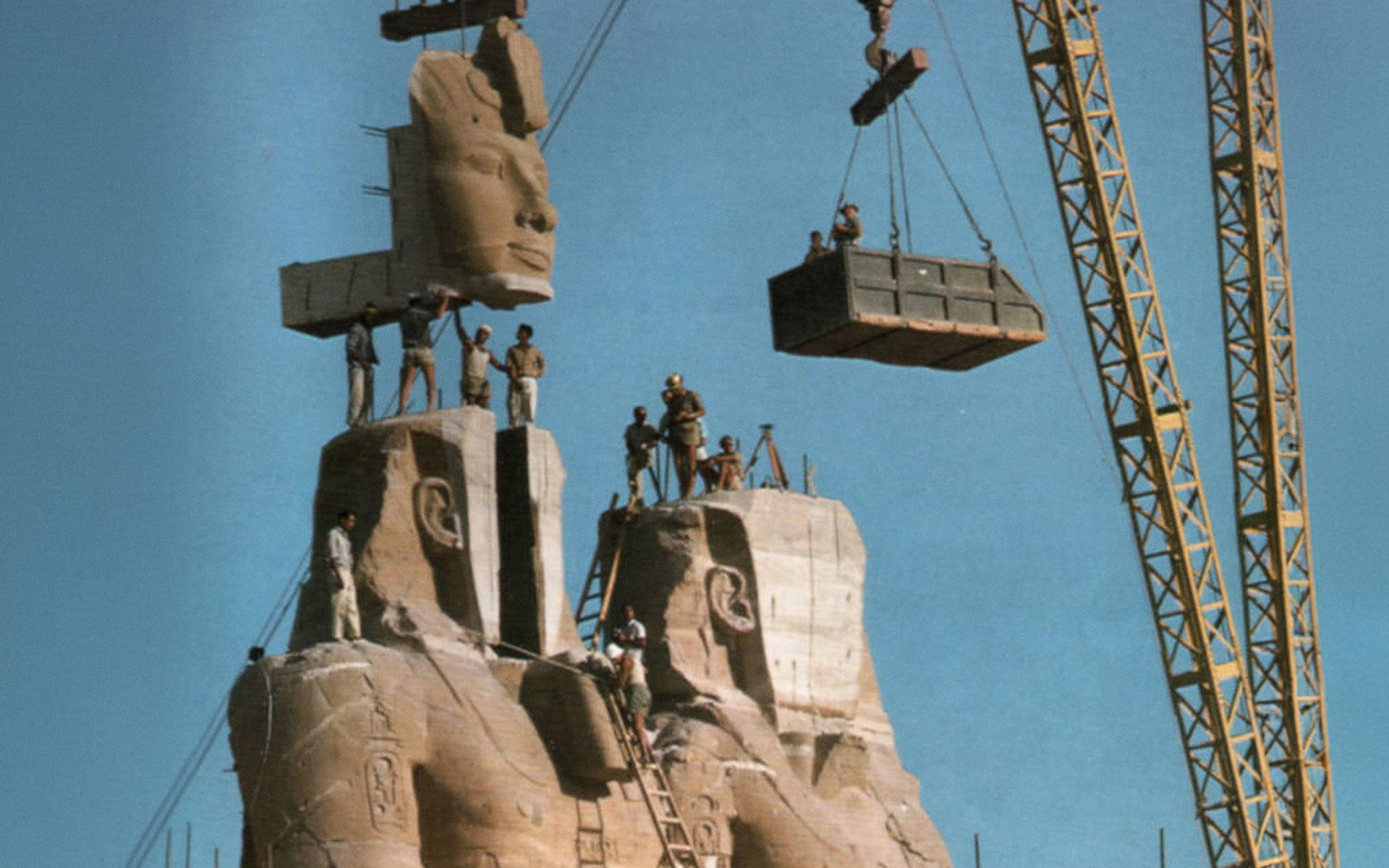
Why use XEPOX
XEPOX epoxy resin boasts several key features making it ideal for demanding applications, such as transporting timber modules:
exceptional adhesive strength, forming extremely strong bonds between timber and steel. Formulated to penetrate deeply into materials, this resin ensures lasting adhesion and excellent mechanical strength.
XEPOX is available in various densities to suit different applications and penetration depths, including XEPOX FLUID, which is particularly suitable for injection into anchor holes.
In addition to XEPOX, Rothoblaas also offers a range of products such as RAPTOR, DISC and WASP, tailored for the timber construction industry.
These cutting-edge technologies, combined with the experience and expertise of trusted partners like Marlegno, ensure the successful completion of even the most ambitious projects, while consistently upholding the highest standards of quality and safety.
Read all about XEPOX here, and for additional transport and lifting solutions, visit this page.
All rights reserved
Technical Details
- Companies:
- MARLEGNO
- Country:
- Any
- Produkty:
- XEPOX F - FLUID